While most of us hope an OSHA inspector never has cause to pull up to our farm, dairy is slowly, but surely, coming under additional scrutiny. An inspection has a limited scope; it is a snapshot - one day from a dairy's yearlong cycle of activity. In a presentation at the Wisconsin Frame Builders Association annual meeting last week, Cheryl Skjolaas, with University of Wisconsin-Madison highlighted key findings from Wisconsin OSHA's Dairy Farm Local Emphasis Program (LEP).
The first inspections took place in January 2012 with a goal to complete 30 inspections by years end. Of the 15 inspections that actually took place, only two dairies were found in compliance.
Within the state of Wisconsin, a "dairy dozen" - 12 items identified by the LEP for field inspections - emerged. While these items, listed below with Skjolaas' comments, were identified as common hazard areas, all producers would be well-served to take a closer look at these pieces of their operation:
The first inspections took place in January 2012 with a goal to complete 30 inspections by years end. Of the 15 inspections that actually took place, only two dairies were found in compliance.
Within the state of Wisconsin, a "dairy dozen" - 12 items identified by the LEP for field inspections - emerged. While these items, listed below with Skjolaas' comments, were identified as common hazard areas, all producers would be well-served to take a closer look at these pieces of their operation:
- Manure storage facilities and collection structure – Manure channels under the barn are considered a confined space. Open-air storage, too, may head down this road one day. It has limited entry/exit points and people are not meant to be there. When backing an agitator in, OSHA wants to see a barrier to block tractor tires from entering, but you must ensure your plan doesn't violate other OSHA standards.
- Dairy bull and cow behavior/worker positioning – Animal handling is a high hazard site. We need to look at barn lighting and the potential for slips, falls, and in winter, employee cold stress. The use of chemicals and pharmaceuticals are the greatest identified risk - but they are also starting to look for handrails and guards where appropriate.
- Electrical systems – Most farms practice lockout procedures but need to add tag out. Dairies must also lessen their reliance on extension cords, which are identified as a high risk.
- Skid steer loader operation – Skid steers do not fall under an agricultural standard; they are powered industrial vehicles. Regardless, all employees need training and records of the training must be maintained.
- Tractor operation – All tractors need ROPS and buckets are not a lift mechanism for people. It is okay to take the ROPS off of stationary tractors - but as soon as that tractor moves they need to be back in place. Seat belt use should also be encouraged, as it is personal protective equipment.
- Guard power take-offs.
- Guarding of other power transmission and functional components – These rules apply more so to farms with grain storage facilities.
- Hazardous energy control while performing service and maintenance on equipment – Lock out is required. Keys should be taken out of the vehicle or tractor. Power, too, should be shut off to all barn fans before performing maintenance on one.
- Hazard communication – Sixty percent of farms had a violation in this area. In Wisconsin the best resource is ATP 60 in the DATCP code for dairy, but a written program is essential.
- Confined spaces – Placards denoting a confined space need to be on the outside of the building, not after the entrance.
- Horizontal bunker silos – The best guidelines for upright silos are from the Silo Association. Limited research has been done on horizontal silo safety.
- Noise – Noise is currently a national emphasis program. Evaluation of hearing loss when working with agricultural equipment is ongoing.
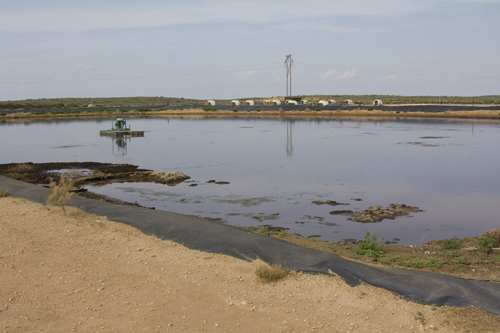