
Ventilation is a key component of barn design. Natural ventilation and tunnel ventilation are two common options for dairy barns. Cross ventilation historically hasn’t been used as much, but it is growing in popularity for dairy cattle housing.
Iowa State University Extension Ag Engineering Field Specialist Brian Dougherty compared ventilation options at a dairy design workshop held in Garnavillo, Iowa.
Both tunnel and cross ventilation are forms of mechanical ventilation. They use fans to pull outside air into the barn. While tunnel ventilation directs airflow parallel to the feed lane, cross ventilation typically goes perpendicular to the feed lane. Dougherty pointed out a benefit is that the air travels parallel to the stalls, which should give better airflow where the cows lie down.
He also explained that barns using cross ventilation can be built wider. While tunnel ventilation works best in barns with less than six rows, cross ventilation can be used in barns up to 24 rows wide. Baffles and fans are necessary to redirect airflow, though.
Whereas tunnel-ventilated barns only have inlets at the end wall or along sidewalls on one end of the barn, cross-ventilated barns have inlets along the entire length of the barn. This provides more evenly distributed air over a greater distance.
It is also easier to control light intensity in a cross-ventilated barn. In tunnel-ventilated barns that also have a natural ventilation option, it is more difficult to disperse light evenly. When hot, cows tend to avoid areas of bright light, which can lead to more bunching in dark areas of the barn.
However, cross-ventilation barns can’t be built with a natural ventilation option. This creates a constant reliance on fans and requires a backup generator in case the power goes out.
Even with the number of fans needed and energy requirements, “Cross-vent barns are actually very competitive cost-wise,” Dougherty said.
Beyond building and operational costs, Dougherty shared some other considerations. One is the type of fans being used.
“Fan selection is huge,” he said. The wrong fan could cost a farm $30 or more per cow per year, he noted.
He also said that poor maintenance and dust buildup can reduce fan efficiency by 50 percent of more. These are factors to keep in mind no matter what type of mechanical ventilation system is used.
If you want to evaluate the performance of your current fans, Dougherty directed farms to visit BESS Lab online. This online publication provides unbiased performance data for over 800 commercially available ventilation fans ranging in size from 8 inches to 54 inches in diameter. The fans are searchable according to size, airflow, ventilating efficiency rating, and manufacturer.
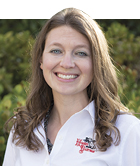
The author is an associate editor and covers animal health, dairy housing and equipment, and nutrient management. She grew up on a dairy farm near Plymouth, Wis., and previously served as a University of Wisconsin agricultural extension agent. She received a master’s degree from North Carolina State University and a bachelor’s from University of Wisconsin-Madison.