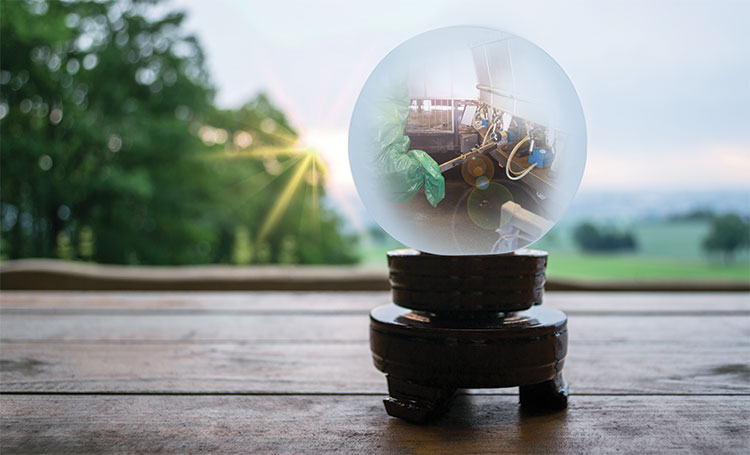
Design considerations we have used for decades could soon be going out the window,” forecasted Tom Haren with AGPROfessionals based out of Greeley, Colo. “We are going to have to unlearn a lot of our current thumb rules.”
Haren should have a good pulse on dairy farm design and location. With 20 years of industry experience, Haren runs a business that functions like that of a commercial real estate developer. Licensed in 15 states, Haren has guided numerous dairy farm families through the dairy startup process and conducted over 100 public hearings to site new dairy farms.
“Right now it takes two to four years to get a new dairy running. That’s from receiving the first telephone call to hanging the first milking unit on a cow,” said Haren.
The costs for these dairies are quite high. As a result those expenses must be spread out over more units. In this case the units are cows.
“The minimum size for a green-field dairy (new construction) is 1,800 to 2,000 cows,” noted Haren. “Most involve 3,500 cows and above.”
Expenses running higher
In the West, dairy farms have been experiencing a longer horizon to recapture investments on new construction projects.
“Regulations, water availability, and an extensive development schedule are among the items adding to cost structures,” said Haren. “Then there is the ongoing expense of securing and retaining a quality farm manager and a competent labor force.”
Water is a big issue for all dairy farms, especially new dairy farms.
“The country can be divided into two water source groups. For most of the West, water either comes from mountain sources or is pumped from underground. Unlike the eastern U.S. where groundwater gets replenished from rainfall, nearly all Western groundwater comes from glacial sources trapped underground thousands of years ago or snow melt from above-ground sources,” explained Haren. “That water isn’t easily replenished.”
It’s the water availability issue that could eventually drive what Haren believes will be two changes . . . trends towards enclosed facilities and more enhanced water treatment systems.
“Enclosed facilities such as tunnel- and cross-ventilated freestall barns require a much smaller footprint than naturally-ventilated counterparts,” noted Haren. “Not only can you better control the environment for the cows, the entire building footprint is much smaller. That makes the facilities faster to build,” he said.
From a nutrient- and water-handling standpoint, there are additional advantages.
“Not only can operators better control rainfall and rainfall impacts, the lagoon size gets smaller,” said the entrepreneur. This discussion naturally leads to wastewater treatment.
“You tell me that the best we can do is dig a hole for a lagoon?” he asked rhetorically.
“One day dairy farms will produce municipal-quality water,” he said in answering his own question.
There will be many drivers to this trend.
“In the West, it can cost between $2 and $4 million to secure water rights for a 1,800- to 3,500-cow dairy,” said Haren. “On the flip side, water treatment systems run between $4 to $5 million,” he said, noting that costs will continue to come down as technology improves.
“As this process unfolds, lagoons will go away,” he predicted. “This will open up a whole new set of locations to site dairy farms.”
Smaller footprints ahead
“The shear footprint necessary to site a dairy also will shrink,” predicted Haren. “Up until now, most dairy farms wanted a minimum of a section of land (640 acres) to site a new dairy. That size requirement has been necessary to locate naturally ventilated freestall barns, lagoons, and have enough nearby land to apply nutrients. In many cases, those building sites also required flatter land, often prime farm ground,” said the real estate and farm-planning specialist.
“In the future, dairies can be built on smaller sites. Water treatment and nutrient recovery systems will reduce environmental impacts,” said Haren. “As this shift unfolds, dairy farms will be built on more marginal land but built closer to grain sources and population centers.”
More robots
The trend toward more automation and more robots will continue to unfold, and even pickup momentum, forecasted Haren.
“This will be a game changer for many reasons. Not the least will be adding more predictability to securing labor and long-term finances,” he went on to say in forecasting that farms will begin to prepay labor through employing robot technology.
Dairy processors will also evolve.
“Quicker, more incremental responses will be the new wave of reacting to dairy markets,” suggested Haren. “Dairies will develop a modular ability to adapt to processors and size will be determined by transportation costs. Farms may even be situated close enough to plants that milk could be piped directly to processors.”
Optimistic thoughts
Haren believes robot and water treatment technology will improve over time. As that technology improves, the costs for it will drop, allowing a lower entry point when considering farm size and cow numbers. That is important for the long-term financial health of the dairy sector, as it should reduce the capital investment for dairy farms. Plus, there is the ongoing issue of farm transfers.
“I have far more buyers for 1,500- to 3,000-cow dairies than 5,000- to 10,000-cow dairies,” he said.
Lastly, Haren offers another optimistic thought . . . “I believe these collective technologies actually may slow the rate of consolidation in our dairy industry.”