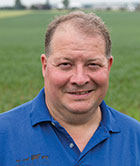
Our first changes back home were in stall dimensions and lunge room. Then we moved into ventilation and cooling, which are still improving. The last limitation to production was resting time due to bedding comfort and maintenance.
Observing my own clients back then, I saw a 15-pound spread in production between those with great comfort and those without. Almost 30 years later, that spread has become 35 pounds.
The common denominator
A major factor has been the use of well-maintained sand bedding. Cow comfort experts have evaluated records and found that the combination of greater milk production, improved somatic cell count (SCC) premiums, reduced clinical mastitis cases, less lameness, and reduced replacement costs due to more longevity result in $2 per hundredweight less costs of production with sand compared to mattresses.
There are areas of our practice territory that dig great sand for bedding out of the hillsides. Those areas are more than two hours from our practice base. Our cost of sand is mostly trucking, and that amounts to $200 per cow per year.
I knew the use of sand bedding would require recycling. There is no engineering textbook for sand separation, so the rest of this article will discuss the important details we learned about sand recycling. Recycled sand may never be as good as new sand, but we can get pretty close.
There are also significant negative effects of not recycling sand:
1. Expense of new sand.
2. Stalls not bedded as well.
3. Farms may try bedding savers, which reduce comfort.
4. Sand in lagoons.
5. Plugged flumes.
Down the lane
We have some mechanical separation in our practice area, but my preferred method is sand separation lanes. Most of our sand lanes have been built out of farmer and builder ingenuity without an engineer.
First timers can make devastating mistakes. Many forget that manure flows downhill. Sand laden manure mixed with water will separate during deceleration. This emulsion needs to be made before separation and is done well in a flume. We have some installations that have a scrape drop right before the separation lanes, and they struggle with sand quality.
Travel speeds of 5 feet per second (f/s) will move sand, and it will separate out below 1.5 f/s. Manure solids will separate out at less than 1 f/s. As sand accumulates in the lane, the flow rate slows down, so the sand needs to be removed daily.
The sand removed is placed on a dewatering floor that has a 3% slope back to the sand lane. We make windrows of the sand, and they are turned weekly for two to six weeks. When piles are turned, more water comes out, and we may leave the bottom portion, which is the wettest, to put on the top on the next windrow. The dewatering floor needs to have capacity for six to eight weeks.
Clean water works best
There are a few of the construction details to consider. Plan to use a skid loader (11-foot wide) or payloader (12-foot wide) to remove the sand. The lane needs to be at least 10 inches deep, but we have some that are 4 feet deep. The deeper ones don’t freeze as easily, but they usually require a reception pit and pump rather than gravity flow into the lagoon.
The overall length of the lane depends some on cow numbers but ranges from 150 to 300 feet long with a 0.25% slope. Many lanes are constructed with hairpins, but straight ones may recover more clean sand.
Cleaner flush water makes cleaner sand. The cleanest flush water comes from a retention pond, but that quickly runs out, requiring drawing water from the closed loop manure system. The cleanest water in that system comes from 2 feet below the surface. Multiple lagoons in sequence will have the cleanest water in the last lagoon.
The cleanliness can be greatly enhanced by installing a weep wall that retains up to 60% of the solids in the upstream lagoon between two lagoons. Slope screens and screw press mechanical separators only capture about 20% of the solids.
Cleaner flush water has less odor. Experts tell us we want the organic matter of flush water to be less than 4%, and 1% to 2% is preferred.
So, how do you get manure out of the barn into the sand lane? Sand chews up components of scraper systems, but we have dairies that have used them for decades. They just plan on replacing parts.
Mechanical scraping with a tractor or skid loader into a flume is a common method in existing barns that have less than 1.5% slope. Flush is the labor saving method preferred for new construction and for barns that were built with more than 1.5% slope.
A flume is usually a 24-inch PVC pipe that runs the width of the barn and to the sand lane. Portions of the top of the pipe are cut out to allow manure to drop in. Don’t cut out all of the top or it may collapse. The smooth inside wall of a culvert has been used as a cheaper alternative, but it is less durable. Do you really want to replace this thing?
The flume should have 0.5% to 0.75% slope for sand. The flume is flushed with water from the lagoon to move the manure to the sand lane. This water creates the emulsion that is separated. Since this water rinses the manure from the sand, it needs to run for some time after the last manure is pushed into the flume.
If the flush water is stopped before the sand is fully rinsed, the manure will not be rinsed out when the flume is restarted. Pumps last longer when they run continuously and the manure system is a closed loop, so thinking a pit is too full to run the system doesn’t make sense.
We first built a sand lane 15 years ago, and now almost every barn constructed in our practice area has sand lanes. Most of the recent ones have been flush barns. Next article, I’ll discuss how flush barns with sand separation have made clean, comfortable, and healthy cows with labor savings. It’s a real win-win-win-win.