The authors are veterinarians with Quality Milk Production Services, Cornell University.
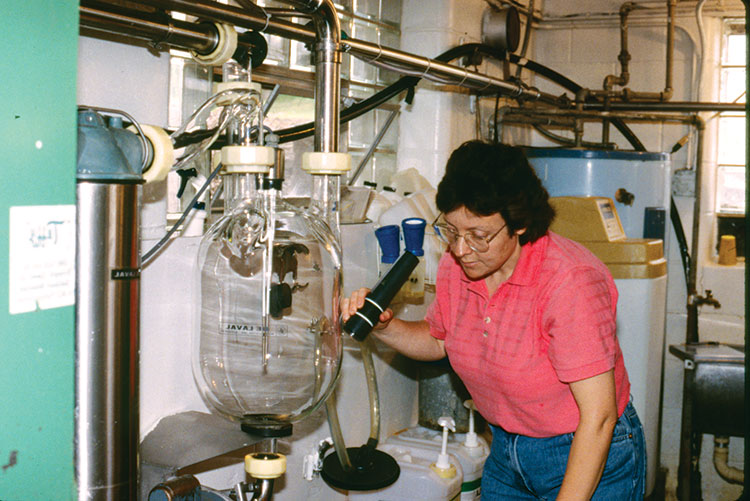
Washing the inside of the pipeline on a milking system involves multiple aspects that should be monitored on a routine basis. Let’s begin with the basics.
The components of washing the pipeline are the same no matter if you are milking in a tie stall barn, conventional parlor, or rotary parlor. Water volume, water temperature, chemical concentration and volume, and slugging and drainage are all required to wash the pipeline properly.
When there is an issue with the wash system, troubleshooting involves monitoring the water temperature of the wash solution, verifying the amount of chemicals dispensed, and checking the chemical activity of the wash solution. However, these components alone are not enough to determine if the wash system is functioning properly or not. Often, the slugging of the wash system is not monitored, but the wash system slug is the single most important component when washing the pipeline properly.
To conserve the water necessary to wash the pipeline, the system is designed to wash by forming a slug instead of simply flooding the entire pipeline. A slug is formed by adding wash solution to the pipeline for a predetermined amount of time in order to achieve a specific volume of water, and then a large amount of air is introduced behind the wash solution. The addition of air pushes the water together and fills the volume of the pipeline in a specific area.
Slug it clean
The slug is then pushed around the pipeline and scrubs all surfaces on the inside of the pipeline. To clean the pipeline properly, the slug should stay together, contacting all surfaces of the pipeline as it travels through the pipeline to the receiver.
As the slug enters the receiver and terminates by hitting the wall, the wash solution will contact all surfaces of the receiver as it breaks apart. This process of the slug breaking apart in the receiver is what cleans the surfaces of the receiver and splashes up into the gooseneck to clean this as well.
A complete slug analysis requires a vacuum analyzer to determine the vacuum drop that the slug creates as it travels through the pipeline. It involves hooking up a vacuum analyzer at the milk inlet closest to the receiver on the add water side of the pipeline and then a second test point at the last milk inlet furthest from the add water line.
The vacuum in the pipeline will drop at each test point as the slug travels by because the slug is filling the entire volume of the pipeline. The vacuum drop at each test point can be determined as well as the time it took the slug to travel from the first test point to the second test point.
The vacuum drop required to maintain the slug and move the slug around the entire pipeline without falling apart is different based upon the diameter of the pipeline. For a 2-inch pipeline, the vacuum drop should be 5 to 11 inches mercury (Hg), and for a 3-inch pipeline, the vacuum drop should be 4 to 8.5 inches Hg.
The total volume of solution needed to wash the pipeline is another important value that should be known. There is an exact volume of wash solution for each milking system, and this wash solution volume is determined by following the guidelines set forth in the “Troubleshooting Cleaning Problems in Milking Systems” from the National Mastitis Council (NMC). If there is too much wash system solution, then one could be using too many chemicals and/or diluting the chemical concentration. On the flip side, if there is not enough wash solution, then the slugging of the wash system will not function properly.
Slug size matters
There is a proper size of the slug and rate of speed at which the slug travels around the pipeline. Ideally, the slug volume should be one-fourth to one-third of the volume of the receiver and travel at 25 feet per second.
An air injector is used to create the slug and move the slug around the pipeline. The air injector off time is the time that the wash solution is added to the pipeline. One can determine the size of the slug if they know the rate at which wash solution is added to the pipeline and by taking the air injector off time.
The air injector on time is the time that the air injector is adding air to the system with the intention of forming the slug and pushing the slug around the entire pipeline to the receiver. By listening during the wash cycle, one can determine the air injector on and off times.
The speed of the slug can be determined by keeping the time from when the air injector turns on until the slug enters the receiver and measuring the distance of the pipeline. The actual slug speed is then verified by analyzing the vacuum recording and the amount of time it took the slug to travel between the two test points.
Listening to and watching the wash cycle can also tell you if there are issues with the wash system. If you hear a “sucking air” sound, that means that the wash solution is being returned to the wash vat at a rate that is slower than the rate at which it is being added to the wash system. If you see wash water building up in the trap to a point where the system traps out, then the size of the slug may be too large. If you see bubbling wash solution in the receiver or trap, then there is an air leak by the trap or receiver and this can impact the rate at which wash solution is returned to the vat.
On a recent wash-up evaluation of a tie stall operation that was experiencing high bacteria counts, the value of doing a full slug flow analysis was reinforced. The producer called for help, stating that his standard plate count was 118,000 colony forming units per milliliter (CFU/mL).
In further discussion on the phone, we requested that he take a sample, after starting with an empty bulk tank, of his bulk tank milk after the first group of cows milked and at the end of milking. A laboratory pasteurized count (LPC) was performed on these samples. At the start of milking the LPC was 700 CFU/mL, and at the end of milking it was 500 CFU/mL. Both of these are above the goal of less than 200 CFU/mL, which signaled he had an equipment cleaning problem.
In further conversation, the question of a slug flow analysis was brought up, and he stated that his dealership had been out and watched the slugs hitting the receiver, and that they looked adequate, but they had not used a vacuum analyzer. We arranged a time to come out and performed a full slug flow analysis.
As shown in the picture below, the vacuum graphs clearly showed that the first half of his pipeline (red line) was not receiving adequate slugs and, therefore, was not being cleaned. With this new information, he had his dealership come back out and adjust his air injector timing in order to produce adequate slugs, and his bacteria count problems returned to low levels.
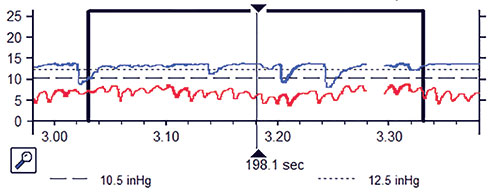
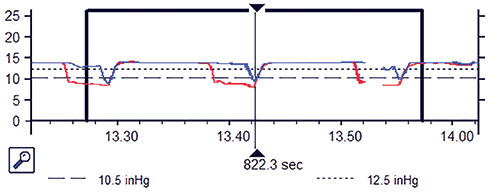
Providing the wash temperature at the beginning and end of the wash cycle, the volume of chemical dispensed, and the active alkalinity, pH, and parts per million (ppm) of chlorine of the wash solution are all important values to know. However, omitting the slug analysis falls short in delivering complete data to the dairy producers when troubleshooting a wash system issue. A stopwatch, thermometer, tape measure, measuring cup, and bucket to catch the wash solution are all that’s needed to begin monitoring your wash system, but be sure to always request a slug analysis to get the complete picture.