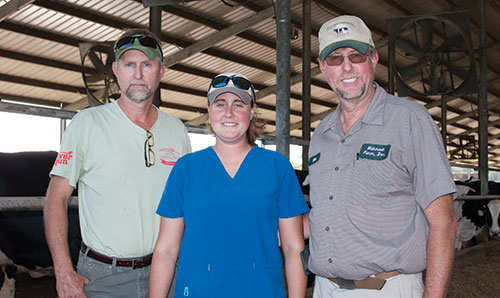
With herd health closely monitored, Hillcrest Dairy only needs every-other-week herd health and reproduction checks, explained Andy, Caitlin and Mark Rodgers.
Everyone who cares for cows knows that keeping cows cool and comfortable in hot and humid weather can be a constant, uphill challenge. Overcoming those conditions in the Deep South makes the endeavor more like climbing a mountain.
For brothers Mark and Andy Rodgers and their respective children, Caitlin (Mark) and Josh (Andy), a new freestall barn constructed in 2009, equipped with many of the latest cooling elements, has made all the difference. So, too, has the farm's cow-care philosophy.
"We follow three rules on our dairy," said Mark of Dearing, Ga., located just a short drive away from the home of the famed Masters golf tournament. "First is cow comfort, second is repeatability and third is manage the exception."
"In our southern climate, cow comfort takes on a whole new twist. We want to remove as many obstacles as possible that impede a cow's ability to be healthy and make milk," said Mark, who heads up animal care along with his daughter Caitlin.
"For starters, we have an east-west orientation of our four-row freestall barn. That barn has 14 feet of additional lane under the shed, allowing freestalls to remain shaded even in the midday sun," Mark explained, noting he modeled the barn after those he saw in Florida. With that shade over the freestalls a constant, fans and soakers help keep cows cool, as all were running on the late October day in which temperatures still pushed past 85°F with humidity to match.
To be economical, the fans start to come on in stages beginning at 68°F, while the soakers begin dispensing water at 72°F for one minute with a 10-minute rest phase. By the time temperatures climb to 84°F, fans are at full power with soakers running water for one minute with a five-minute rest phase.
"Heat and humidity are our enemies in Georgia, and we need to do everything possible to combat them," noted Mark.
No headlocks and rubber flooring throughout are two additional features in Hillcrest Dairy's freestall barn.
"We wanted to remove any obstacle that could impede feed intake, that included no headlocks," said Mark. "We are able to sort cows with our DeLaval identification system as individuals leave the parlor," he added. As for working with cows in between milkings, each side of the four-row barn has a sort gate system designed to catch cows on either side. The engineering essentially allows one person to sort cows.
As cows approach the corner of the freestall pen, a gate can be swung open, inviting cows into the drovers lane. Once a cow proceeds to that area, the gate between the pen and drovers lane can be shut and the handler then works the cow to the end of a pen and guides the animal to an area with a second gate. Once past the second gate, the cow proceeds through a permanent pen structure and then to a headlock. As the cow's head passes the headlock opening, a tug on the rope closes the latch and the herdsperson can begin working on the cow.
"We use this system to conduct all of our fresh cow work and perform 50 percent of our A.I. breedings," stated Caitlin. As the cow care specialist explained cow handling, it was very evident that every fresh cow gets special attention. The protocol for Bovikalc, Cydectin, trim switch and two ear tags was written on top of the gate with permanent black magic marker. "If someone has a day off, then everyone knows the protocols," she explained.
Rubber eliminates synch breedings
The floors in the entire freestall barn are lined with rubber belting.
"At one time we were a grazing dairy, and we bred cows off of standing heats. We were hoping to do the same after we moved into the freestall barn," said Mark sharing his vision. "The rubber belting helped us gain higher peak milks and the cows show more standing heats with the sure footing."
"To check for heats, we study activity from our DeLaval system and use our eyeballs to find cows in heat," added Caitlin. As for the heifers that are on pasture a few miles from the farm, the Rodgers plan to install a pasture-based Alpro system to track heats there as well.
This is also where the third goal comes into play . . . manage the exception.
"Low daily milk weight, low-activity cows are my greatest concern," says Caitlin. "Getting ahead of the curve has helped us get past 30,000 pounds of milk.
"Any cow that is one, two or three standard deviations from herd activity gets closely looked at throughout the day with those two or more standard deviations off getting even more attention," she said of the system her father added to the farm in 2012 in anticipation of Caitlin's return to the dairy. "Those on the low end most likely have a health issue while those on the high side are likely coming into estrus," said Caitlin.
As for the repeatability rule, "It's our goal to bore our cows to death," said Mark. "Cows can never have too much routine."
That has helped the herd get to its recent 31,800-pound herd average. So, too, has forage quality. "Feed has been a limiting factor for us in Georgia, as the hot summer days cause plants to lay down more lignin (when compared to more northern climates) that erodes digestibility," said Mark's brother Andy, who heads up crops. "To constantly combat that dilemma, we have to do everything to maximize quality. That is one reason we always keep a years supply of corn silage on hand in our six pit bunker silos," he said. "That allows for complete fermentation and maximum starch availability," he added.
"We also triple cover those pits with three types of covers. The first layer is a vapor barrier, the second a traditional black-white plastic, and the third top layer of a vinyl netting (pest barrier) is to control animals such as crows, raccoons, wild hogs and other feed thieves," said Andy. The farm is able to get three crop harvests in the southern climate. Forage crops include corn silage, ryegrass and brown midrib sorghum.
Unique to Hillcrest
Having been a closed herd since 1974, the farm has excellent hoof health and has been fortunate to not have hairy heal warts on its dairy. That being the case, the Rodgers don't run footbaths and usually only trim hooves at dry-off. Prior to building the freestall barn, the Rodgers had some issues with bruised heels, mainly from stones. That resulted in culling 32 cows the final year of grazing. The very next year, housed in the rubber-lined freestall barn, the Rodgers culled only two cows for feet and leg issues.
Active on social media, Mark heads up the Hillcrest Farms Inc., Facebook page that is followed by nearly 4,000 people. "From my perspective, you can never make enough posts about baby calf videos or cows using brushes in the freestall barn," said Mark. "People really eat that up online."
Brother Andy is also a very innovative welder. And that being the case, the entire Handy Hint page in this issue (see page 167) features Handy Hints from Andy and Mark.