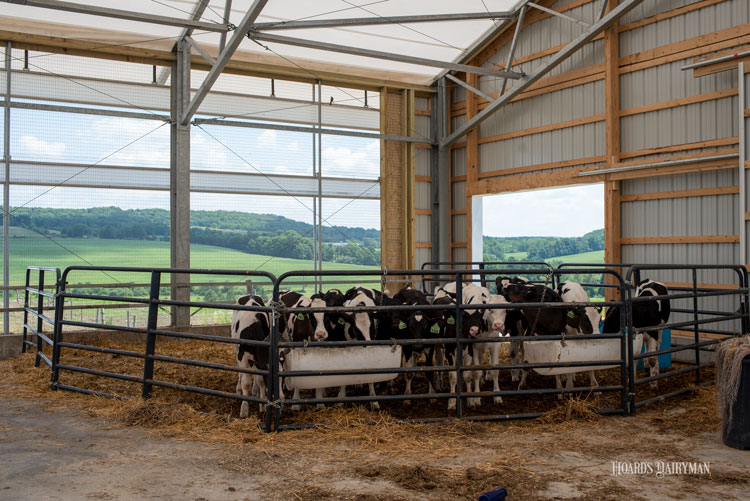
Natural ventilation is used successfully in many dairy barns, and it has been for years. As our dairy farms grow and as milk production climbs, some may wonder whether natural ventilation will be able to keep pace.
John Tyson, a Penn State agricultural engineer, addressed this topic during the Penn State Dairy Nutrition Conference. “How far can we push natural ventilation in modern dairy housing?” he asked. “Can natural ventilation achieve what we need it to?”
He explained that dairy cattle barns are getting wider, and there are more animals living in those shelters. In addition, farms may have more barns or buildings on the same property, potentially blocking some airflow.
“When animals are brought indoors, the conditions inside need to be equal to if not better than conditions outside,” he said. Tyson noted that our current goals for ventilation are to provide clean, dry air to animals throughout the year; remove moisture, gases, and pollutants; and remove excess heat produced by animals during hot weather.
He explained that natural ventilation is dependent on natural winds around the shelter and temperature differences from inside to outside, while mechanical provides air exchange using properly sized fans and inlets.
The three elements that drive natural ventilation are:
- Building orientation
- Size of the inlets
- The building’s exposure to natural wind
For orientation, Tyson said a building placed perpendicular to prevailing winds makes natural ventilation a better option.
“Wind exposure is very important,” he said. Tyson anticipates new barns in the future will be built at higher sites with better elevation to capture as much natural wind as possible.
He also reminded that separation between buildings is really critical, and that ideally, there would be 256 feet between buildings to maximize wind exposure. He shared that an upwind obstruction can disturb airflow 5 to 10 times its height.
Tyson said another big driver for natural ventilation is barn sidewall height. Over several decades, dairy facilities went from 10-foot-tall walls with a 2-foot opening to today’s barns with wide-open sidewalls of 14 feet or taller. The goal, Tyson said, is to have 11 square feet of inlet opening per cow, counting only one side of the barn as the inlet.
Looking forward, the goals for ventilation will remain the same. “Cows are going to still need fresh air and removal of moisture, heat, gases, and pollutants,” Tyson said. Farms may monitor ventilation more precisely, though.
Tyson foresees more emphasis being placed on consistency of air quality in the shelter, with farms utilizing automated controls and artificial intelligence to run these ventilation systems to maximize consistency.
Productive cows are hotter cows
He also believes there will be more of a focus on heat removal from the shelter and heat abatement for individual cows.
“With higher production comes more heat,” Tyson said. He explained that a cow milking 100 pounds per day has a heat stress threshold about 10 degrees lower than a cow milking 75 pounds. “High-producing cows are going to be heat stressed earlier in the summer, earlier in that heat curve, than lower-producing cows,” he said. “Heat abatement is an area we are going to have to put more emphasis on in the future, not less.”
Natural ventilation may be able to fit our needs in some dairy barn situations, but Tyson sees a combination of natural and mechanical ventilation as an opportunity for other facilities. While mechanical ventilation is more costly to operate, it is more consistent and could be used to supplement natural ventilation when needed to keep up with cows’ needs in the future.