
In the last issue, we examined the variation in waiting time for cows to be milked in a free-flow robot facility. We were concerned that some cows have very prolonged waiting times due to competition at the robot entry way and that this extended period of waiting would negatively impact lying time, which it does.
There are several possible contributing factors that would promote extended waiting times to access the robot in automated milking system (AMS) herds. Previously, we discussed the impact of parity and robot entry design. Other possibilities include stocking density relative to the robot and the type of traffic system.
How many cows per robot?
Since robots are expensive, manufacturers often attempt to defray the cost over as many cows as possible, resulting in larger groups and subsequent growing competition around the robot. Advancements in robot arm technology can lead to reduced box times and increases in the “theoretical robot capacity.” The theoretical robot capacity for a herd with an average box time of seven minutes per cow and 22 hours of robot availability per day (assuming one hour wash cycles twice per day) would be:
- 60 minutes per hour/seven minutes per cow = eight cows milked per hour
- 22 hours x eight cows milked per hour = 176 milkings per day
- 176 milkings per day/2.8 milkings per cow per day = 63 cows per robot
Since this is a common box time, we frequently see about 60 cows per robot in the industry. However, if box time was reduced to six minutes with faster unit attachment, the same calculation would result in 78 cows per robot. The cost of the robot defrayed over an additional 15 cows makes the economics more appealing. However, such calculations fail to understand that cows are not robots and that there is a circadian rhythm to robot use throughout the day as shown for a free-flow robot barn in Figure 1.
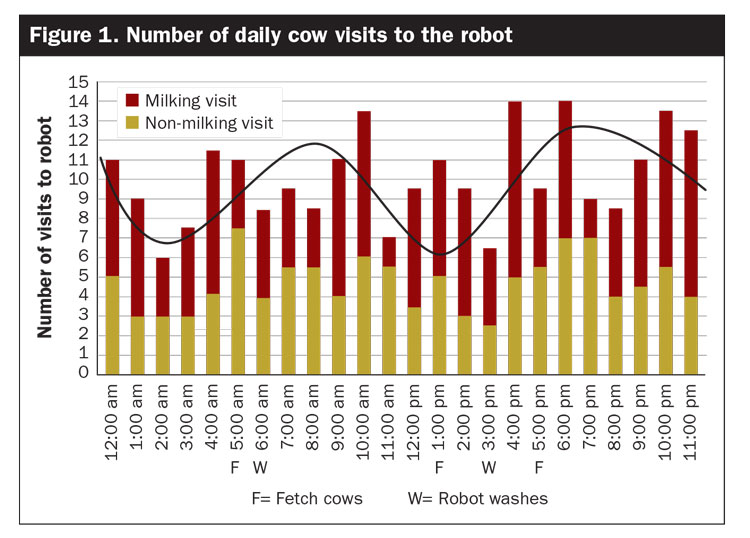
The desire to be milked is not constant throughout the day, with busy times around dawn and dusk and quiet times early in the morning and around midday. Therefore, it is highly unlikely that cows will maintain the constant throughput required to achieve the theoretical robot capacity. That is why in the literature, we see optimal cow performance at about 55 cows per robot.
To further optimize performance, we favor two to three robots per pen as this appears to result in more milk per robot, reduces competition between cows, improves labor efficiency, and gives producers maintenance options.
Directing traffic
In addition to the number of cows per robot, another potential factor influencing waiting time is the traffic system chosen for the AMS facility. We examined daily waiting time to be milked in the robot in a common guided-flow layout we typically see in the Upper Midwest with one “tollbooth” robot at the end of a 60-cow, tail-to-tail, two-row freestall pen. Cows are sorted into a commitment pen in front of the robot or to the feedbunk, depending on the duration of time since last milking.
We used a combination of gate data and video to determine average daily waiting times to be milked for two pens of cows in a milk-first guided-flow system. What we found was a nearly identical pattern to what we saw in the free-flow dairy.
Some cows are very efficient and spend very little time waiting in the commitment pen, while other cows spend very long periods of time waiting. The mean daily waiting time was identical to the free-flow system at 90 minutes per day. This was a little shorter than the mean time we typically see in parlor herds milking three times per day where cows typically wait for a mean of two hours and 20 minutes per day. However, the main concern is the cow that waits for extended periods of time — far longer than we would see in a parlor milked herd. We observed cows waiting over 3.5 hours per day, with one cow waiting nearly eight hours per day (Figure 2).

In the free-flow herd we observed, the extended waiting time was due at least in part to competition between first-lactation heifers and older cows in the same pen and the design of the robot entry way. There was no parity effect in the guided-flow herd as first-lactation heifers were grouped separate from mature cows in the facility. The problem cows may have been subordinates within the group or perhaps lame cows struggling to compete with other cows.
For that reason, we recommend that in guided-flow herds, the commitment pen is not the same as the fetch pen. Pens should be designed so that we can gather cows struggling to access the robot into a fetch area within the commitment pen so that they would have priority access to the robot and would not have to compete with other cows waiting in the commitment pen.
Another option we recommend for guided-flow herds is to set an alert for cows that have passed through the sort gate into the commitment pen but have not entered the robot within some set period of time — perhaps 30 minutes. Then the herdsperson would be alerted to the fact that there is a cow struggling to enter the robot and could assist.
Giving cows a guide
As has been found in previous studies, our survey data suggests that, while guided-flow systems may result in slightly less milk per cow per day on average than free-flow systems, there are some attractive benefits over free-flow systems, including lower pellet feed rates (about 3 pounds less per cow per day), lower fetch rates (5% versus 8%), and less labor (about half a minute per cow per day). There is, of course, great variation within each traffic system, and the focus should be on optimal design and management for whichever system is chosen.
Risk for extended waiting times in guided-flow commitment pens is a real concern that needs to be addressed through alerts. Another concern is restricting access to fresh feed delivery at the feedbunk, which may limit intake and curb milking performance in cases where there is too much competition at the sort gate. For that reason, we prefer to leave crossovers open in the pen, even if there are guided-flow gates around the robots.
We refer to this system as semi-guided or hybrid flow. It is an approach we are starting to see more of in the industry and one that helps alleviate some of the welfare concerns around restricting access to feed in guided-flow systems.
Whether a free-flow or guided-flow system is used, waiting times can be reduced with proper planning of the robot area, pen design, appropriate stocking rate, and management. This allows cows more time in their day to rest, eat, and just be cows.