Financially speaking, last year was one of the dairy industry's best. While most equipment purchases were made this past fall, some last-minute changes to the fleet may be in order before haying gets under way.
When making the decision to replace or upgrade hay equipment, aside from price, producers should consider how the new piece or pieces of equipment fit into their current hay making system, notes Dennis Hancock, University of Georgia, in the Midwest Forage Association's Forage Focus.
In a hay making system, each piece of equipment needs to match the size and field efficiency of the other pieces (see tables). Even if just one piece is not as efficient as the others, it can create a bottleneck. Such slowdowns elevate the risk for rain damage, lower forage quality and elevate costs per ton.
Regardless of the farm, generalizations can be made as to what equipment will minimize the number of man-hours needed to make the amount of hay required, adds Hancock. The first step is to get a handle on the amount of hay needed. Once this is determined, the number of hay acres and cuttings can be estimated.
After these figures are calculated, comparisons of field efficiency need to be considered. When dealing with cutting, tedding and raking, productivity is determined in acres per hour (Table 1). Hay baling depends primarily on the raking step to ensure a sufficiently sized windrow that allows the baler to function efficiently.
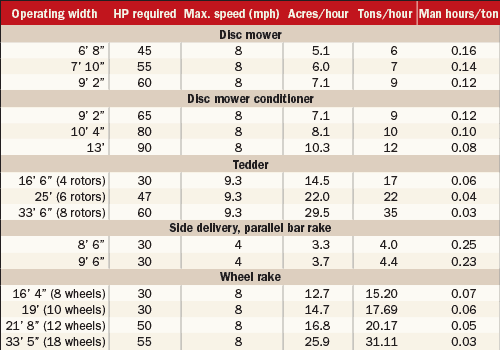
When comparing efficiency of baler options (Table 2), focus on tons of hay baled per hour.
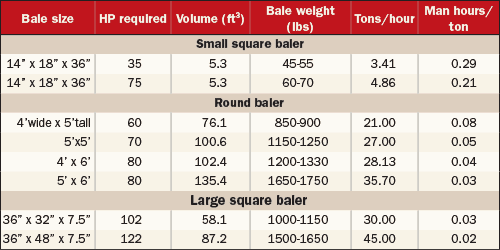
Though the field efficiency values shared by Hancock are estimates, they can be useful in comparing equipment. Before making an investment in a new piece of hay-making machinery, look beyond the price tag. Consider how the implement will fit in your system, whether or not it will match your other equipment and its potential to save time.

The author , Amanda Smith, was an associate editor and is an animal science graduate of Cornell University. Smith covers feeding, milk quality and heads up the World Dairy Expo Supplement. She grew up on a Medina, N.Y., dairy, and interned at a 1,700-cow western New York dairy, a large New York calf and heifer farm, and studied in New Zealand for one semester.
When making the decision to replace or upgrade hay equipment, aside from price, producers should consider how the new piece or pieces of equipment fit into their current hay making system, notes Dennis Hancock, University of Georgia, in the Midwest Forage Association's Forage Focus.
In a hay making system, each piece of equipment needs to match the size and field efficiency of the other pieces (see tables). Even if just one piece is not as efficient as the others, it can create a bottleneck. Such slowdowns elevate the risk for rain damage, lower forage quality and elevate costs per ton.
Regardless of the farm, generalizations can be made as to what equipment will minimize the number of man-hours needed to make the amount of hay required, adds Hancock. The first step is to get a handle on the amount of hay needed. Once this is determined, the number of hay acres and cuttings can be estimated.
After these figures are calculated, comparisons of field efficiency need to be considered. When dealing with cutting, tedding and raking, productivity is determined in acres per hour (Table 1). Hay baling depends primarily on the raking step to ensure a sufficiently sized windrow that allows the baler to function efficiently.
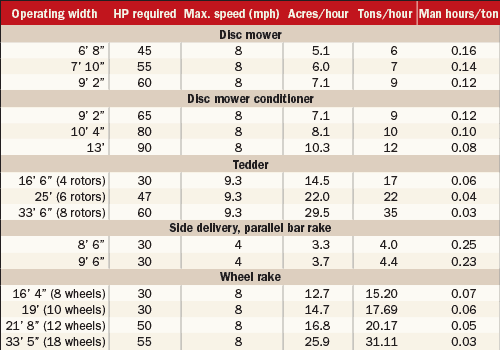
When comparing efficiency of baler options (Table 2), focus on tons of hay baled per hour.
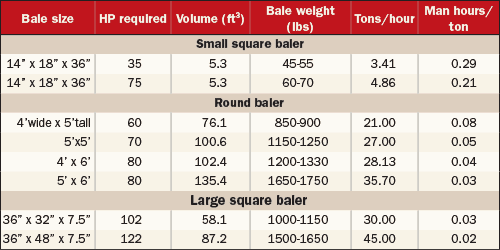

The author , Amanda Smith, was an associate editor and is an animal science graduate of Cornell University. Smith covers feeding, milk quality and heads up the World Dairy Expo Supplement. She grew up on a Medina, N.Y., dairy, and interned at a 1,700-cow western New York dairy, a large New York calf and heifer farm, and studied in New Zealand for one semester.