The author is a dairy technical services specialist at Diamond V, Cedar Rapids, Iowa.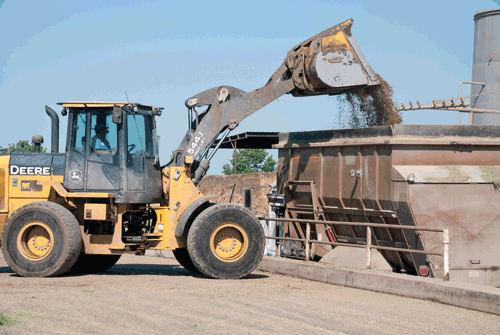
Feed costs make up nearly 50 percent of your total cost of milk production, and that is assuming your cows are getting the correct nutrition at the right time. Not mixing TMRs correctly or not delivering them on time will cost you milk which will bump up feed cost per unit of milk.
We have conducted nearly 200 TMR audits across the U.S. since January 2008. An audit is an on-farm evaluation of the feed storage, feed preparation, mixing, and delivery. It is designed to evaluate critical factors affecting TMR consistency and offer solutions to improve efficiency of feeding.
Here are some common problems that make TMRs inconsistent:
Don't overfill mixers
This is one of the most common things we see. We find it in both vertical and horizontal mixers.
You do not have to overfill the mixer very much to cause variation. Most often when we can cut the weight of an overfilled load back 10 to 20 percent, we see noticeably less variation in the TMR measured either with the Penn State Shaker box or with lab analysis. Generally, we see about half as much variation in key ration components when there is no overfilling.
The downside of cutting batch sizes is that the feeder has to make more loads which can be an issue if the feeder is already stretched for time. You have to weigh the risk of lost production and compromised rumen health with inconsistent TMRs versus greater labor and diesel costs to make more mixer loads. Nutritionists and dairymen often tell us they see their cows perform better when the TMR is less variable.
Particularly in vertical wagons, worn augers and blades are conditions that hurt your ability to process long-stem hay and straw effectively so that TMR particle size is adequate to prevent sorting. Worn-out edge deflectors (kicker plates) on the bottom flighting in vertical units and worn-out augers in horizontal units cause the mixer not to mix efficiently. Research has shown that, as the mixer wears, it requires more mixing time to get a consistent TMR. However, most feeders do not take the extra time to allow good mixing as the mixer wears.
Most manufacturers recommend we mix 2 to 3 minutes after the last ingredient is added. Most often, the mixer is running while all of the ingredients are loaded. However, many times we see the feeder shut the mixer off and deliver the TMR without mixing the last ingredient which usually is corn silage or a liquid supplement. As the load gets overfilled and as the mixer wears, the undermixing creates even more inconsistency in the TMR.
Loading liquids carefully
Liquid supplements are a very important part of maintaining TMR uniformity. Liquids help prevent sorting and can be used for low-inclusion products such as minerals and feed additives. However, I have seen very inconsistent TMRs when liquid supplements are loaded in the front or back of twin-screw vertical wagons and even in horizontal wagons when there is not enough mixing after liquid was added.
Loading the liquid in the front of a twin-screw vertical wagon caused more material to end up on the middle screen of the Penn State Shaker box at the front of the load (beginning of unloading) and less at the end of the load (end of unloading). When we moved the wagon ahead about 4 to 5 feet and added the liquid between the two screws of a twin-screw wagon, the TMR became very consistent from one end of the bunk to the other. The dairy owner reported 1 to 2 pounds more milk in his herd within one to two weeks after he started loading the liquid in the middle of the wagon.
On another dairy, we did some lab analysis on a TMR where the liquid supplement was loaded in the back of a twin-screw vertical wagon. The liquid supplement was 20 percent protein on a dry matter basis. There was a consistent rise in moisture and protein levels in the TMR as we move from the front to the back of the wagon (from the beginning of unloading to the end). The supplement should have been added to the middle of the mixer.
Mind the silo face
We know moisture and nutrient levels can change dramatically from top to bottom and from side to side in silage piles and bunkers. Testing moisture levels frequently and adjusting silage inclusion levels will keep dry matter intakes more consistent. However, it is becoming apparent that we cannot keep up with the variation in silage faces and make the appropriate changes in the TMR to maintain consistent intakes and milk production. One approach to minimizing variation in dry matter intake and milk production involves a three-step process of facing the silage piles.
The steps are:
• Face all of the silage needed for feeding.
• Push the silage into a central pile which enables mixing of the silage to reduce the variations in moisture and nutrients.
• Sample from the central pile for moisture testing and lab analysis.
Dairies that have adopted this strategy to make the silage more consistent have reported more consistent intakes in their herds.
Feed delivery time
We conducted a TMR audit for three consecutive days on a large dairy in the Upper Midwest. It was extremely cold, and on the second day feeding was delayed nearly two hours because tractors would not start, doors on the TMR wagons would not open during unloading, and feeders were fueling payloaders during feeding time. The "Ah Ha moment" came the next morning when we observed a large amount of weigh back for the late-fed pens. It all of a sudden occurred to us that these cows were shorted two hours of feeding, causing the greater weigh back.
It is critical to feed pens of cows as close to the same time every day as possible so that dry matter intake stays as consistent as possible. One way to monitor feeding times is to use feed tracking software that will record TMR drop times for each pen. You should review this every week to see if your feeders are staying on time. Talk to the feeders to see if they are getting disrupted by truck drivers delivering hay and commodities to the dairy or if the feeder is trying to do other jobs during feeding.
We have found the TMR audit to be a very successful tactic to help dairies get more consistent with their feeding programs. Most dairies only require minor modifications in their feeding program to get better intakes, more milk, and healthier cows.
Click here to return to the Nutrition E-Sources
110325_202
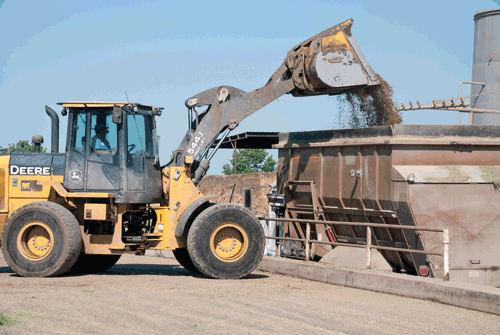
Avoid overfilling, one of the most common mistakes that keep TMRs from being as consistent as they can be. Add any liquid in the middle of the mixer, not the front or the back.
Feed costs make up nearly 50 percent of your total cost of milk production, and that is assuming your cows are getting the correct nutrition at the right time. Not mixing TMRs correctly or not delivering them on time will cost you milk which will bump up feed cost per unit of milk.
We have conducted nearly 200 TMR audits across the U.S. since January 2008. An audit is an on-farm evaluation of the feed storage, feed preparation, mixing, and delivery. It is designed to evaluate critical factors affecting TMR consistency and offer solutions to improve efficiency of feeding.
Here are some common problems that make TMRs inconsistent:
Don't overfill mixers
This is one of the most common things we see. We find it in both vertical and horizontal mixers.
You do not have to overfill the mixer very much to cause variation. Most often when we can cut the weight of an overfilled load back 10 to 20 percent, we see noticeably less variation in the TMR measured either with the Penn State Shaker box or with lab analysis. Generally, we see about half as much variation in key ration components when there is no overfilling.
The downside of cutting batch sizes is that the feeder has to make more loads which can be an issue if the feeder is already stretched for time. You have to weigh the risk of lost production and compromised rumen health with inconsistent TMRs versus greater labor and diesel costs to make more mixer loads. Nutritionists and dairymen often tell us they see their cows perform better when the TMR is less variable.
Particularly in vertical wagons, worn augers and blades are conditions that hurt your ability to process long-stem hay and straw effectively so that TMR particle size is adequate to prevent sorting. Worn-out edge deflectors (kicker plates) on the bottom flighting in vertical units and worn-out augers in horizontal units cause the mixer not to mix efficiently. Research has shown that, as the mixer wears, it requires more mixing time to get a consistent TMR. However, most feeders do not take the extra time to allow good mixing as the mixer wears.
Most manufacturers recommend we mix 2 to 3 minutes after the last ingredient is added. Most often, the mixer is running while all of the ingredients are loaded. However, many times we see the feeder shut the mixer off and deliver the TMR without mixing the last ingredient which usually is corn silage or a liquid supplement. As the load gets overfilled and as the mixer wears, the undermixing creates even more inconsistency in the TMR.
Loading liquids carefully
Liquid supplements are a very important part of maintaining TMR uniformity. Liquids help prevent sorting and can be used for low-inclusion products such as minerals and feed additives. However, I have seen very inconsistent TMRs when liquid supplements are loaded in the front or back of twin-screw vertical wagons and even in horizontal wagons when there is not enough mixing after liquid was added.
Loading the liquid in the front of a twin-screw vertical wagon caused more material to end up on the middle screen of the Penn State Shaker box at the front of the load (beginning of unloading) and less at the end of the load (end of unloading). When we moved the wagon ahead about 4 to 5 feet and added the liquid between the two screws of a twin-screw wagon, the TMR became very consistent from one end of the bunk to the other. The dairy owner reported 1 to 2 pounds more milk in his herd within one to two weeks after he started loading the liquid in the middle of the wagon.
On another dairy, we did some lab analysis on a TMR where the liquid supplement was loaded in the back of a twin-screw vertical wagon. The liquid supplement was 20 percent protein on a dry matter basis. There was a consistent rise in moisture and protein levels in the TMR as we move from the front to the back of the wagon (from the beginning of unloading to the end). The supplement should have been added to the middle of the mixer.
Mind the silo face
We know moisture and nutrient levels can change dramatically from top to bottom and from side to side in silage piles and bunkers. Testing moisture levels frequently and adjusting silage inclusion levels will keep dry matter intakes more consistent. However, it is becoming apparent that we cannot keep up with the variation in silage faces and make the appropriate changes in the TMR to maintain consistent intakes and milk production. One approach to minimizing variation in dry matter intake and milk production involves a three-step process of facing the silage piles.
The steps are:
• Face all of the silage needed for feeding.
• Push the silage into a central pile which enables mixing of the silage to reduce the variations in moisture and nutrients.
• Sample from the central pile for moisture testing and lab analysis.
Dairies that have adopted this strategy to make the silage more consistent have reported more consistent intakes in their herds.
Feed delivery time
We conducted a TMR audit for three consecutive days on a large dairy in the Upper Midwest. It was extremely cold, and on the second day feeding was delayed nearly two hours because tractors would not start, doors on the TMR wagons would not open during unloading, and feeders were fueling payloaders during feeding time. The "Ah Ha moment" came the next morning when we observed a large amount of weigh back for the late-fed pens. It all of a sudden occurred to us that these cows were shorted two hours of feeding, causing the greater weigh back.
It is critical to feed pens of cows as close to the same time every day as possible so that dry matter intake stays as consistent as possible. One way to monitor feeding times is to use feed tracking software that will record TMR drop times for each pen. You should review this every week to see if your feeders are staying on time. Talk to the feeders to see if they are getting disrupted by truck drivers delivering hay and commodities to the dairy or if the feeder is trying to do other jobs during feeding.
We have found the TMR audit to be a very successful tactic to help dairies get more consistent with their feeding programs. Most dairies only require minor modifications in their feeding program to get better intakes, more milk, and healthier cows.
110325_202