The author is the director of dairy policy analysis at the Center for Dairy Profitability, Madison, Wis.
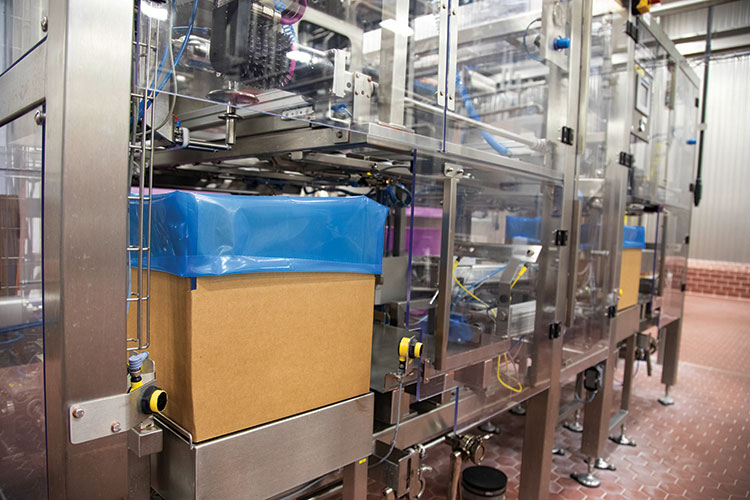
We are beginning to see the term “make allowance” in dairy headlines, and it is important to understand what it means and how it works. In the simplest terms, a make allowance is an estimate of what it costs to transform milk into a finished dairy product like butter or cheese. These estimates are important because the values are used by USDA in setting the monthly minimum prices that regulated plants must pay for the components in your milk checks.
What is a make allowance?
An example of a make allowance is shown in the product price formula below where your butterfat value is determined by the sale price of butter. The butter price is tabulated in the monthly weighted average of a mandatory survey of dairy plants across the country that produced and sold butter. This report is published weekly on Wednesdays and is called the National Dairy Product Sales Report (NDPSR).
Butterfat Price = (Butter price - 0.1715) x 1.211
There are two values, or parameters, in the formula that you may not recognize. The first is the 0.1715 number, which is referred to as the “make allowance.” The other number is the 1.211 value, which is called the “yield factor.” The make allowance, 17.15 cents in this case, is the estimate of what it costs to transform milk into a pound of butter. The yield factor of 1.211 indicates that you can make 1.211 pounds of butter from one pound of butterfat. Remember, most U.S. butter is only 80% butterfat, with the rest being water and other milk solids.
What is the problem?
Because products like butter have a “standard of identity,” the yield factors are unlikely to drift over time or change very often. However, processing costs in plants do change, and 14 years have passed since the make allowance was last examined with eventual updates to the formulas via action through the Federal Milk Marketing Orders.
Make allowances do not include the costs of milk or other dairy ingredients, but they do include plant factors such as labor, utilities, nondairy ingredients (like salt or cultures), packaging, testing, and so forth. These allowances don’t include costs of storage, transportation, marketing, or other pre- or post-processing expenses for these dairy products.
Dairy processors can get trapped by these product price formulas. Because we reverse calculate milk prices from dairy product sales, manufacturers don’t actually know what they will have to pay for milk from a dairy farmer until the dairy processor has brought it into their plant, made and sold their products, reported those sales to USDA, and the Federal Milk Marketing Orders have made the monthly announcement of prices. More simply stated, if the make allowances are insufficient to cover the costs of the products sold, the plants would lose money and go out of business over time.
Is there evidence that a problem actually exists?
The Federal Orders do not guarantee a profit to processors. If processors cannot function within the make allowances, they have four choices: control their costs, lower their premiums paid, depool their milk and no longer be subjected to regulated minimum prices, or go out of business.
If a single plant’s costs are not competitive in the long run, they will have to go out of business. Alternatively, plants may be able to restore a margin by lowering their voluntary premiums paid to producers, especially if their competitors have done the same.
If premium reductions are not enough, then a manufacturing plant can choose to depool their milk from the Federal Order and no longer be bound by the minimum prices. If premiums decline over time and depooling becomes more common, these pressure relief valves are indicating a problem with the make allowances.
Solve one problem, create another problem?
Increasing the make allowances may be needed to reflect the higher costs of processing. However, doing that will shift the problem from processors to producers. You can see in the butterfat price formula that raising the make allowance from 17 cents to 19 cents, for example, will actually reduce the regulated butterfat price.
Over time, a lower price for butterfat and the other components of milk will cause less to be produced, and fewer products will be available for consumers. If product supplies are somewhat constrained, the prices paid by consumers will inflate. This will get captured in the NDPSR and fed back through the product price formulas, helping to restore butterfat prices.
The updating process
Changes to the make allowances and product price formulas will come through a Federal Order hearing. At this hearing, evidence will be provided from individual processors regarding how their costs of processing have changed. There will also be other testimony offered.
For instance, I have conducted a cost of processing study which is available at https://DairyMarkets.org/cop/. Dairy farmers and their representatives will offer testimony that will be recorded into the transcript of the hearing record.
The USDA will have to sift through all of this evidence and make a recommended decision, which could be no change . . . or it might be to increase the make allowances. But, the final decision is still in the hands of dairy farmers and their organizations who will vote to approve or discard the amended Federal Orders.
There are no simple changes to our milk pricing system. However, the entire industry must be healthy for all segments to thrive. Right now, lower premiums and depooling are suggestive that dairy manufacturers are having problems under regulation. It is time for the industry to have that discussion on make allowances.